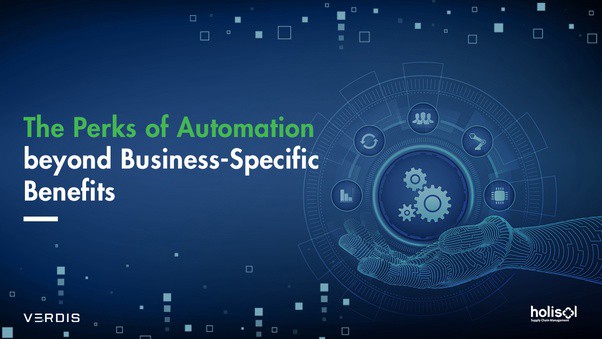

For most organisations, planning for complex supply chain processes, including dispatch and production planning, involves a team of planners and long planning times. With planning optimisation, plans are automated, delivered faster, and efficient (cost and fulfilment optimised).
But, what does automation imply for the workforce?
Positive Employee Experiences
The importance of having a human touchpoint for creating rich customer experiences, or human cognitive and creative skills for product and process-level differentiation is well understood. When manual and repetitive tasks are automated, new roles and responsibilities that are focused on problem-solving, exception handling, contingency planning, communication, etc. emerge. These create better and more satisfying employee experiences, professional growth, and greater engagement with the organisation.
To understand how Verdis planning optimisation delivers positive business and employee outcomes, let us know your interest for a demo here Artificial Intelligence for Leadership.