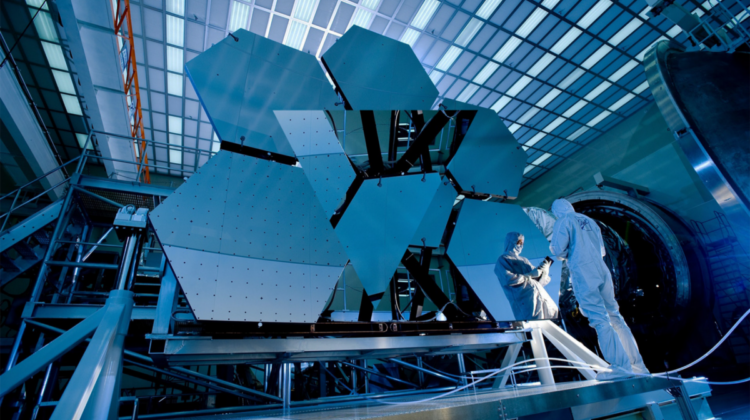

Manufacturing methods continue to evolve. Companies that implement the latest technologies are enjoying increased efficiency, thanks to reduced downtime, fewer defects, and streamlined processes. The advantages come from an interconnected manufacturing facility with access to advanced monitoring and analytics. Connecting, automating, tracking, and analysing are now key practises for successful manufacturing.
Connecting New and Legacy Equipment
The latest innovations in machine learning (ML), artificial intelligence (AI), and automation rely on interconnected devices and equipment. Connected manufacturing equipment can communicate with central data acquisition systems and human-machine interfaces (HMI).
Some of the newest manufacturing equipment features electronic components for monitoring and analysing machine data. Even legacy equipment can be part of an automated factory. Equipment that is 20 or 30 years old may still run well. Replacing the equipment, retraining staff, and disrupting daily operations are costly processes.
Older equipment may still have a few decades of service life, decreasing the cost-effectiveness of replacing them with newer internet-connected machines. However, older machines can be retrofitted with the industrial internet of things (IIoT) sensors and other monitoring equipment.
The retrofitting process provides an affordable way to adopt the latest IIoT technologies. The connections allow for a wide range of applications in manufacturing and other industries. Companies can monitor the performance and output of machinery and automating or augmenting tasks.
For example, a leading commercial property developer in the UK retrofitted its heating and cooling systems with IoT sensors, resulting in a 42% reduction in energy consumption and providing workers with 24/7 monitoring.
Automation and Labour Augmentation
An interconnected factory or manufacturing site can augment or replace manual labour. Modern manufacturers now benefit from the latest developments, including augmented reality (AR), wearable technology, and a vast range of scanners and sensors. These technologies are helping workers perform their jobs safer and more efficiently. In some cases, the technology can entirely replace the need for human labour.
A completely autonomous “lights-out” factory is not a new concept. FANUC, a Japanese robotics company, began operating a factory with no human labour in 2001. However, factory automation and AI have come a long way in the past two decades.
Many assembly line tasks are now automated and completed by robotics or IIoT-connected machinery. Most of the human labour is devoted to monitoring the equipment instead of performing manual tasks.
An automated manufacturing facility offers a wide range of advantages, including:
● Increased safety
● Lower labour costs
● Increased productivity
● Enhanced product quality
● Reduced lead time
The use of machines to perform dangerous tasks goes back to the beginning of the industrial revolution. However, AI and other technologies are allowing companies to automate even more tasks. The most dangerous and repetitive tasks are often the first to be automated. Replacing manual labour with machines limits the need for workers to perform potentially hazardous tasks, increasing workplace safety.
Reducing the need for manual labour reduces labour costs. Automating tasks reduces the risk of human error. Manufacturers can maintain smaller workforces while increasing output, productivity, and product quality. With more efficient manufacturing processes, businesses can reduce the lead time for new orders, which offers greater flexibility for meeting demand.
Increasing Efficiency with Big Data
Along with connecting and automating equipment, modern technologies allow manufacturers to track and analyse data from machines. Manufacturers can now digitise every aspect of the manufacturing process, from research and development (R&D) to production and supply chain management.
During resource planning, AI helps to optimise the gathering of supplies and equipment. During production and assembly, AI and monitoring equipment help to decrease downtime and improve quality assurance (QA).
The ability to improve manufacturing processes requires accurate data tracking. Sensors and scanners collect data from assembly-line equipment and track every stage of manufacturing. The acquired data is typically sent to a centralised data centre or storage solution. Depending on the needs of the manufacturer, data may be accessed by a variety of software or devices.
For example, workers may monitor the data on a workstation. However, the biggest advances in manufacturing come from the analysis of big data. After acquiring large volumes of data, AI software or ML software may help to improve various manufacturing processes.
Some of the current use cases of AI and ML in manufacturing include:
● Predictive maintenance
● Automated quality checks
● Digital twins
● Supply chain management
● Increased automation
By monitoring the output and performance of equipment, the software can predict when machinery requires maintenance. Improving predictive maintenance helps cut downtime and increase the lifespan of the connected equipment.
AI software can also perform automated quality checks of machinery and products. Artificial intelligence and machine learning technologies can detect the smallest flaws and defects. Catching defects quickly and correcting the issues leads to reduced waste and fewer delays.
Digitising every process and piece of equipment allows manufacturers to create “digital twins.” Digital twins are virtual representations of manufacturing units. AI and ML software can analyse the digital twin to optimise processes before physically starting assembly.
Along with connected equipment, manufacturers rely on connected departments. AI software aids supply chain management by improving communication channels among departments, including warehousing. AI improves inventory management, helping manufacturers automatically account for changes in demand and inventory.
Implementing additional automation also becomes easier. Adding new robotics to support or replace the human workforce involves less of a logistical challenge if the facility is already set up to track and analyse data.
The flexibility provided by AI and ML technologies also allows manufacturers to make changes to products to meet the needs of customers. Smaller production runs become more cost-efficient as manufacturers can easily adjust manufacturing processes to alter products. For example, a manufacturer may produce an increased variety of design options for a product.
Conclusion
The future of manufacturing includes more reliance on data and digitisation. Every stage of manufacturing can be digitised, tracked, and analysed to increase efficiency and produce higher quality products. While automation is not new to manufacturing, artificial intelligence (AI) and machine learning (ML) bring additional levels of optimisation.
The latest technologies allow for greater automation, reduced delays, lower costs, and fewer human errors. Companies that fail to adopt these technologies may struggle to remain successful in the coming years.